Molding with Bentonite Mixture
This method is ideal for castings weighing from 0.1 kg to 120 kg, with the production of piano frames allowing a maximum weight of up to 230 kg. The bentonite mixture is prepared in a wheel mixer and then distributed to individual workstations, where it is compacted into a molding frame. The model device is then removed, and after thorough cleaning with compressed air and, if necessary, the installation of cores, it is moved to the casting area. For mold preparation, we use aluminum or steel (sheet metal) molding frames with sizes ranging from 500 x 300 x 160 mm to 3000 x 1800 x 230 mm, allowing us to meet a wide range of requirements. Typical products of this technology include castings of channel elements, piano frames, and rope pulleys.
Molding with Self-Setting Inorganic Geopolymer Mixture
This technology is suitable for more technologically demanding and heavier castings weighing from 30 kg to 500 kg. The molding mixture is prepared in a continuous mixer SPARTAN 5P and directly poured into molding frames, which have dimensions from 580 x 580 x 390 mm to 1750 x 1200 x 200 mm. After partial setting, which takes approximately 60 minutes, the molds are disassembled and left to harden until the next day. The following day, the molds are coated with a graphite alcohol-based paint and prepared for casting. After pouring and cooling, the mold is disassembled, and the remaining mixture is regenerated for further use. This method is primarily used for producing castings for printing machines.
Thanks to the variability of molding frame sizes and the choice of self-setting geopolymer or bentonite mixtures, we can flexibly respond to the diverse needs of our customers. Hand molding in our foundry allows the production of high-quality castings in small series or individual pieces.
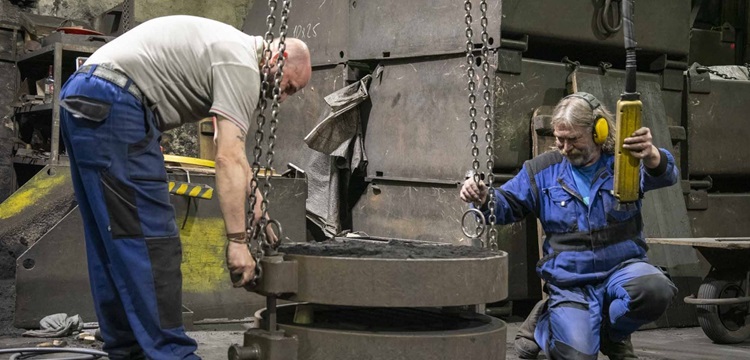