Melting device
The foundry utilizes modern Inductotherm induction furnaces, which have replaced traditional cupolas. Melting in electric induction furnaces ensures cleaner operation with a high degree of flexibility and a conversion efficiency of up to 98%, contributing to the maximum efficiency in liquid metal production. Induction allows for reliable and rapid melting of both gray and ductile iron, with low energy consumption and high homogeneity of the molten metal.
- Nové Město nad Metují Foundry
Melting Department
Induction melting system VIP DUAL TRAK + with a power output of 1000 kW, manufactured by INDUCTOTHERM, is installed on an elevated furnace platform. The robust and durable DURALINE-type furnaces with a capacity of 1000 kg are equipped with a fume hood that captures emissions produced during the melting process, including fugitive emissions. The furnaces are also equipped with an adiabatic cooler to cool the VIP converter during extreme summer temperatures exceeding 30°C.
Charging of the furnaces is done manually from charging boxes on the furnace platform, which are pre-prepared according to the required recipe. Modification of ductile iron is carried out using the ladle pouring method, while inoculation of the iron is performed using the in-mould method. The molten metal is poured into a drum furnace placed on a rail conveyor, which transports the ladle to the casting area. To achieve the desired mechanical properties of the castings, we control and monitor the solidification of the melt through thermal analysis installed on the furnace platform.
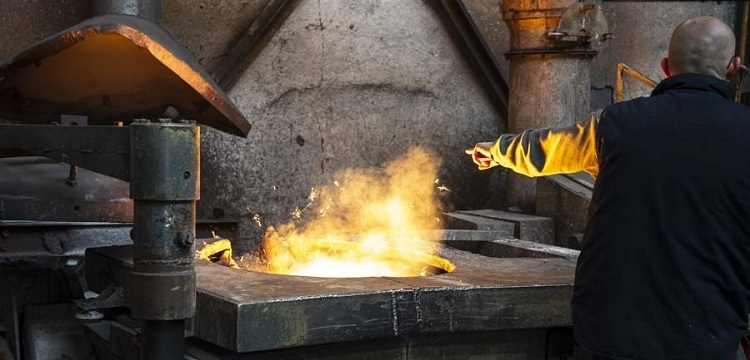