From the earliest attempts to produce metal objects, founders needed a mold that would define the shape of the future product. Due to its availability, workability, and relative stability, wood became the natural material for making these patterns. Although modern technologies bring new possibilities, wooden patterns remain the treasure of every traditional foundry and a testament to the craftsmanship of our ancestors.
History of Wooden Patterns
Throughout the Middle Ages and the Industrial Revolution, the art of making wooden patterns was perfected and passed down from generation to generation. Pattern makers were highly valued craftsmen who had to perfectly understand not only woodworking but also casting technology, metal shrinkage, and casting procedures.
Historically, hardwoods such as oak, beech, or ash were primarily used for pattern making, ensuring resistance to wear and dimensional stability. Softer woods like linden or poplar were used for less stressed parts or for core boxes. Each pattern was a unique piece, handcrafted with extraordinary precision and attention to detail.
The production of a wooden pattern was a time-consuming process that required perfect knowledge of wood as a material. The pattern maker had to account for the natural properties of wood, such as shrinking and swelling, and therefore often used techniques such as cross-grain lamination or combining different types of wood to ensure maximum stability. Larger patterns were made from several pieces carefully joined using tenons, dowels, and other traditional joinery methods.
Technical Aspects of Wooden Patterns
The production of a quality wooden pattern requires consideration of several key factors. The pattern maker must primarily account for the shrinkage of metal during solidification, which means that the pattern must be somewhat larger than the final casting. The degree of shrinkage varies according to the type of metal - from approximately 1% for cast iron to more than 2% for some aluminum alloys.
Another technical challenge is the design of draft angles, which allow easy removal of the pattern from the mold without damaging the molding sand. These draft angles typically range from 1-3° and must be applied to all vertical surfaces of the pattern. The pattern must also include machining allowances in places where the casting will subsequently be machined.
The surface treatment of wooden patterns also plays a key role. Traditionally, patterns were coated with special pattern-making varnishes that protected the wood from moisture and provided a smooth surface that facilitated the removal of the pattern from the mold. The practice of color-coding different parts of the pattern was also common - for example, red indicated cores or cavities, while black or blue marked the main body of the pattern.
Current Value of Wooden Patterns
Currently, despite technological advances, wooden patterns remain a valuable asset of traditional foundries. Their value lies not only in the material but primarily in the craftsmanship, precision, and historical know-how they contain.
Traditional foundries often own hundreds or even thousands of wooden patterns, which represent a true treasure and operational capital for the company. In foundry accounting, these patterns figure as significant assets, sometimes reaching values of millions of crowns. Patterns for classic products, such as piano frames, artistic castings, or technical components, were often created decades ago, and their replacement would be extremely expensive.
Wooden patterns also have the advantage of being relatively light and easily repairable. Damaged parts can be replaced or repaired, thus extending the life of the pattern by additional decades. This longevity makes wooden patterns not only a technological but also an economic tool that is worth carefully preserving and maintaining.
Pattern Making Craft in Modern Times
Although modern technologies like CNC machining have brought higher precision and repeatability to pattern production, manual production of wooden patterns is still used especially for large and simple shapes or for small batch production. Experienced pattern makers can produce a pattern faster and more economically than programming and setting up a CNC machine, especially for prototypes or one-off production.
Modern pattern shops today often combine traditional procedures with new technologies. Pattern design is done using CAD software, but the actual production may still be manual, using modern tools and materials. In addition to traditional woods, materials such as artificial wood, epoxy resins, or polyurethane blocks are now used, offering greater dimensional stability and easier workability.
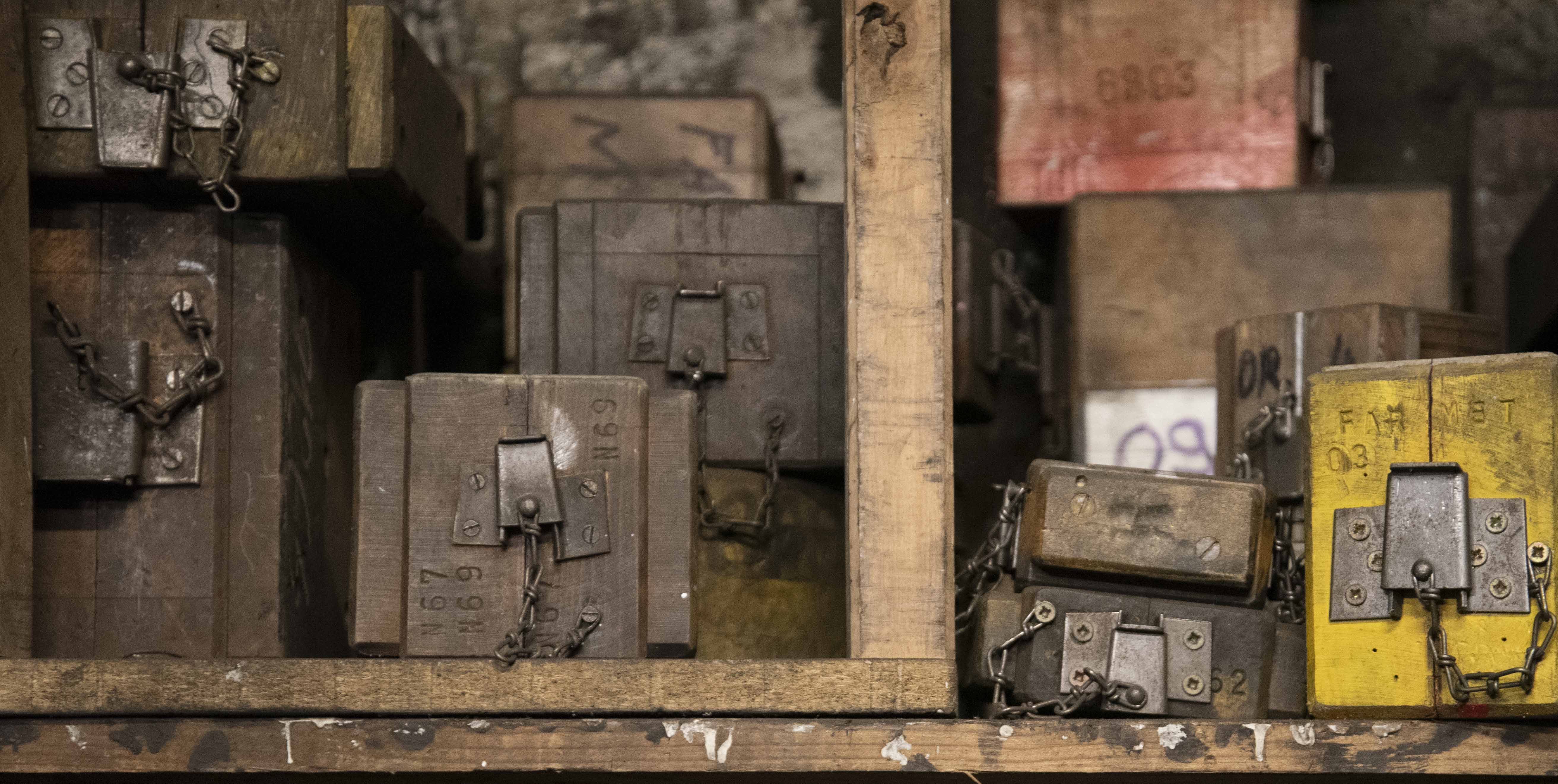
Despite technological advances, the role of the pattern maker remains irreplaceable. Their experience and feel for the material allow them to create patterns that not only meet technical requirements but are also economically advantageous and practically usable in foundry operations.
Emergence of New Technologies
With the advent of additive technologies, especially 3D printing, pattern making is entering a new era. 3D printing allows the creation of complex patterns without the need for complex machining, with high precision and in a relatively short time. For prototypes and small series, 3D printing can be more economical than traditional production.
Current 3D printers can work with various materials, from plastics through resins to metal powders, allowing the creation of patterns with different properties according to specific requirements. Some materials for 3D printing are specially developed for foundry purposes and can even be used directly to create a combustible pattern that burns out during casting (known as lost pattern casting).
However, despite these advantages, wooden patterns have several irreplaceable advantages - primarily long lifespan, resistance to thermal stress during molding, and the ability to absorb moisture from the molding sand. These properties make wooden patterns still relevant even in the era of digital technologies.
The Future of Pattern Making
The future will likely bring a hybrid approach, where traditional foundries will combine their historical wooden patterns with modern technologies. Some parts of the patterns may be manufactured using 3D printing, while the basic structure will remain wooden.
Digitization of existing wooden patterns using 3D scanning represents another way to preserve valuable historical know-how while taking advantage of modern technologies. Scanned patterns can be archived in digital form, ensuring their protection against loss in case of damage to the original. At the same time, digital data can be used to produce new patterns using CNC machining or 3D printing.
Research in the field of new materials for pattern making also continues. Composite materials are being developed that combine the advantages of wood with the properties of modern polymers, such as dimensional stability and moisture resistance. These materials could replace traditional wood in some applications in the future, especially where high precision and repeatability are required.
Significant Pattern Making Traditions in the Czech Republic
The Czech Republic has a rich tradition of foundry work and associated pattern making. Historically significant foundries such as ČKD, Škoda, or Vítkovice Ironworks had their own pattern shops, where dozens of highly qualified pattern makers worked.
Currently, this tradition is maintained not only by large industrial foundries but also by smaller specialized companies, such as the Foundry in Nové Město nad Metují. These foundries often preserve historical patterns that represent not only operational necessity but also cultural heritage.
Pattern making education also has its tradition in the Czech Republic, whether at secondary vocational schools or in the form of apprenticeship training. These educational programs are modernizing today and include both traditional techniques and modern technologies, preparing a new generation of pattern makers for the challenges of the 21st century.
Cultural Value
For traditional foundries such as the Foundry in Nové Město nad Metují, wooden patterns represent not only an operational necessity but also part of cultural heritage and craft tradition. They represent the continuity of foundry art and remain silent witnesses to the industrial history of our countries.
Some historical patterns even have the value of works of art - especially those created for artistic castings, sculptures, or architectural elements. These patterns often required not only technical knowledge but also artistic sensibility and skills close to woodcarving.
In a time when many production processes are standardized and automated, wooden patterns represent a reminder of the value of human dexterity, patience, and craftsmanship that cannot be fully replaced by any technology. Their preservation and documentation is an important task not only for the foundries themselves but also for institutions dealing with industrial heritage.
Conclusion
Wooden patterns are a fascinating connection between the past and future of foundry work. Although new technologies offer alternative paths, wooden patterns remain an important part of traditional foundry work. Their value lies not only in practical use but also in the craftsmanship and historical heritage they represent.
For foundries such as the one in Nové Město nad Metují, these patterns represent a true treasure - they are capital that allows continuation of the tradition of quality production, and at the same time a testimony to the skills and knowledge of previous generations of pattern makers. In an era of rapid technological change, wooden patterns remind us that some values, such as quality, patience, and craftsmanship, remain timeless.
- ONLINE sale of artistic castings- Zdeněk Veitz