It is an iron-carbon alloy where the carbon content exceeds 2.14%, which leads to the precipitation of free carbon in the form of lamellar graphite in the metal matrix.
Gray Cast Iron
From a metallurgical perspective, gray cast iron is characterized by its heterogeneous structure formed by a metal matrix (usually ferritic, pearlitic, or a combination thereof) and graphite lamellae. These graphite lamellae, whose morphology resembles flakes, give the cast iron its characteristic gray fracture color, from which its name is derived. The chemical composition of gray cast iron typically includes carbon in the range of 2.5–3.5%, silicon 1.0–3.0%, manganese 0.4–1.0%, phosphorus 0.05–1.0%, and sulfur 0.05–0.15%. Silicon acts as a strong graphite-forming element that promotes the precipitation of carbon in the form of graphite. Manganese, on the other hand, stabilizes the pearlitic structure and increases the strength of the matrix. The phosphorus content is especially important for increasing the fluidity of cast iron into complex mold shapes, which is crucial particularly in the production of thin-walled and artistic castings.
Mechanical Properties
The mechanical properties of gray cast iron are strongly dependent on its exact chemical composition, cooling rate during solidification, and the resulting microstructure. Key properties include compressive strength of 600–1200 MPa, tensile strength of 100–350 MPa, elastic modulus of 75–160 GPa, and Brinell hardness of 150–300 HB. The characteristic lamellar shape of graphite acts as natural stress concentrators, which explains the relatively low tensile strength and almost zero ductility. However, this aspect is balanced by other advantageous properties: excellent damping capacity that suppresses vibration and resonance, good thermal conductivity (42–50 W/m·K), low coefficient of thermal expansion, excellent machinability, good resistance to wear and seizure, and acceptable corrosion resistance under normal atmospheric conditions.
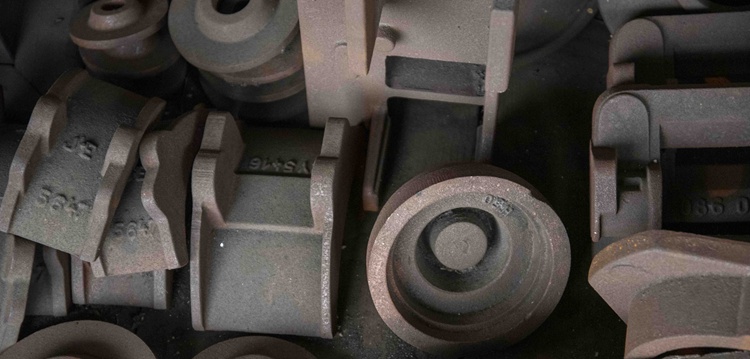
Production of Gray Cast Iron
The industrial production of gray cast iron is carried out by melting a charge composed of cast iron scrap, pig iron, steel scrap, and alloying additives. Melting is performed in various types of melting units: cupola furnaces, which are traditional and economically advantageous equipment for large production volumes; electric induction furnaces, which provide better control over chemical composition and temperature; and rotary furnaces, which are less common but suitable for specific applications. The casting temperature of gray cast iron ranges from 1300–1450°C, which is favorable in terms of energy requirements for production. Casting is most often done into sand molds, which allow for economical production of even complex shapes. According to European standards, gray cast iron is designated as EN-GJL followed by a number indicating the minimum tensile strength in MPa. The most common grades are EN-GJL-150 (formerly ČSN 42 2415), EN-GJL-200 (formerly ČSN 42 2420), EN-GJL-250 (formerly ČSN 42 2425), EN-GJL-300 (formerly ČSN 42 2430), and EN-GJL-350 (formerly ČSN 42 2435).
Applications of Gray Cast Iron
Gray cast iron finds application in a wide range of industrial sectors due to its economic advantages and specific properties. In engineering, it is used for machine tool frames due to its excellent damping properties, cylinders and pistons of hydraulic systems, gearboxes and bearing housings, base plates, and machine beds. In the automotive industry, it is used for engine blocks and cylinder heads, brake drums and discs, parts of exhaust systems, and gears. In construction, it finds applications in sewer pipes and fittings, structural elements such as columns and beams, grids, grates, and covers. In the energy sector, it is used for parts of boilers and heat exchangers, components of water and steam turbines, radiators, and heating elements. In artistic and architectural applications, gray cast iron is used for railings, fences and decorative grids, garden furniture, historical reconstructions, and renovations.
The Future of Gray Cast Iron
Although gray cast iron is being replaced in some applications by modern materials such as ductile iron, composites, or light alloys, its economic advantages and specific properties ensure its continued use in many industrial sectors even in the 21st century. Gray cast iron remains, despite its historical origin, an important structural material in modern industry. The combination of relatively low production costs, good machinability, excellent damping properties, and thermal conductivity makes it the optimal choice for a range of applications where extreme requirements for strength and toughness are not imposed. In the current concept of sustainability and circular economy, it also excels with its 100% recyclability, which further strengthens its position in the portfolio of industrial materials.
- ONLINE sale of artistic cast iron- Zdeněk Veitz